

赵勇:从普通电工到“江苏工匠”
发布时间:2024-01-26 11:14:41
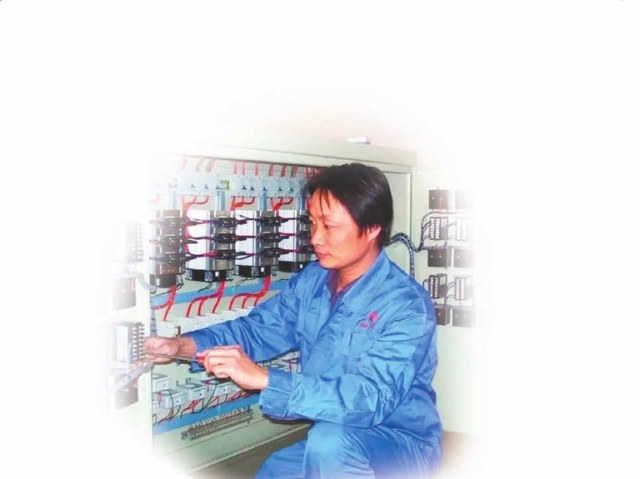
一位普通电工凭着自己的理想信念和孜孜不倦的刻苦钻研,竟攻克了全行业的技术难题。他就是江苏省劳模、“江苏工匠”、南通回力橡胶有限公司副总经理赵勇。
1994年7月,赵勇从南通技校毕业后便就职于南通回力橡胶有限公司,当上一名普通电工。他干一行爱一行钻一行。电加热脱硫罐是生产再生橡胶的一道重要工序。一次,工人在清理脱硫罐内杂料时,发现有几个脱硫罐罐体钢板有起鼓现象。赵勇立即跟踪查找原因,很快查出鼓块是电加热不均匀所致。他认为,罐体凹凸不平带病运行,潜伏着安全隐患。于是,他到安徽淮南脱硫罐生产厂家进行了解,发现很多使用厂家也反映类似问题。生产厂家一时束手无策,拿不出解决的好办法。经了解,罐体过烧现象是全国再生胶行业面临的一个共同难题。
只要有决心,没有过不去的火焰山。回到厂里,赵勇马不停蹄,一头扎进这一难题的研究上。看现场,查资料,问计于工人;严排查,细分析,常常至半夜。功夫不负有心人,很快找出了问题症结:加热不匀是电力控制点位过少所致。厂家设计脱硫罐一般只有两个检测控制点位,检测控制点位过少,造成各区域加热不均匀,致使部分罐体过烧起鼓。在厂领导的支持下,他从增加点位入手,大胆进行技术革新,4个、6个、8个、10个……边增点位,边搞试验。同时对加热系统进行设计改造,采用智能型控制系统自动加热保温。最后将加热点位增加到18个,使整个罐体外壁上下的温度更加均匀,从而有效防止了脱硫罐钢板的过烧现象。这一技术改造大大节约了能源和设备费用,每年为企业减少成本支出100多万元。安徽淮南生产厂家获悉后喜出望外,厂长带领技术人员立即赶来取经,感谢他们解决了一大难题。2010年起,该技术就在全国橡胶再生利用行业全面推广,获得同行业的好评。
“要做就要做最好。”2005年,赵勇又大胆进行工艺创新,将丁基胶由脱硫罐加热改为螺杆翻转加热,这样,不仅节能降耗,而且可大大减轻劳动强度。在公司领导的大力支持下,他与团队成员团结合作,攻克了温度不稳定、螺杆推动不协调等一个个难题:螺杆由开始的单杆改为双杆,直径由7.5厘米增加至12.5厘米,运转方向由同向改为反向。经过几年的探索研发,这一新工艺获得成功,达到了国际先进水平。与老工艺相比,产能一下提高了6倍,每吨耗电量减少一半,直接节约电力成本840多万元。2007年,该技术获得国家发明专利,被国家发改委、科技部、环保总局认定为国家鼓励发展的资源节约和环境保护先进技术。该技术生产的产品,出口到世界50多个国家,为企业年增加销售收入3亿多元,创利2000多万元。
接着,赵勇又参与废橡胶高温常压再生工艺、废橡胶连续脱硫系统、炼胶机辊筒轴承智能化保护装置等新技术、新工艺的研究开发,均获得成功。其中,《废橡胶高温常压再生工艺》获得国家发明专利,另有10多个项目获得国家实用新型专利。这些新技术新工艺的研发成功,使产品的质量和企业效益得到明显提高。他参与设计的动态脱硫罐尾气排放自动控制,使工作环境得到净化和改善,获得行业协会的推广。
南通市海门区总工会供稿